Refractory Selection For Centrifugal Glass Wool Furnaces
Date:2015-10-08 23:22 From:Zhengzhou Sunrise Refractory Author:sunrise
Centrifugal glass wool is a type of cotton-like material made by fiberizing melted glass liquid and then coating with thermosetting resin through centrifugal blowing process. Because of the special composition and manufacturing process of centrifugal glass wool, the refractory selection for the melting furnace of centrifugal glass wool is important.
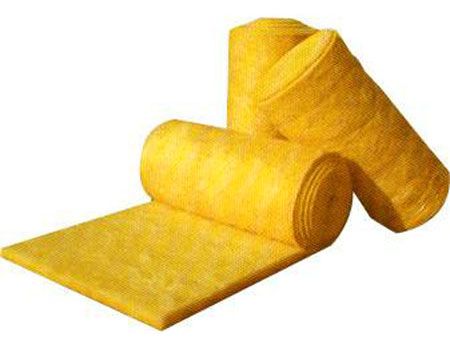
Centrifugal glass wool is kind of low boron glass. Since it has high content of alkali and boron which are easy to volatilize, the refractory materials are subjected to severe corrosion. Furnaces for manufacturing centrifugal glass wool include horseshoe flame kiln, unit kiln and cross-fired kiln.
Compared to other types of furnaces, horseshoe flame kiln features high melting rate, energy saving and easy control. The drawbacks are short service life. The checker works of the regenerators are easy to be corroded and blocked.
The unit kiln covers small areas and has a long service life. It is easy to adjust its manufacturing process. However, it has high energy consumption, serious pollution to environment and low production capacity.
The cross-fired kiln is suitable for the manufacture of glass wool of large-tonnage and multi production line. Since the market of glass wool is not big, cross-fired kiln is seldom used.
The most economic and reasonable design of furnaces is to make the corrosion of refractory materials in different parts synchronous. The selection of refractory materials for different parts is as following:
1)The sidewall of the melting zone
In the melting zone, the melting temperature is low, generally not more than 1400℃, and the glass liquid is viscous, thus the corrosion of sidewall is not quite severe. Fused cast AZS 33# is generally used here. In the cross-fired kiln, in order to expand the service life, AZS brick containing 30% ZrO2 is used.
2)The breast wall of the melting zone
The breast wall is in the flame space. Due to the high-temperature air and the reaction between the bricks and alkali and boron adhered on the surface and gaps of the breast wall, the breast wall is corroded. Thus, neutral and basic refractory materials with good high temperature stability and good resistance to alkali and boron are used.
3)The bottom paving block of the melting zone
In order to reduce the heat loss, insulation materials are used in the bottom. However, insulation causes the increase of temperature and accelerates the corrosion. Fused cast AZS is preferred in the bottom. When bubbling technology is used, it greatly accelerates the mechanical erosion of the bottom blocks. The traditional fused cast AZS paving block cannot meet the requirement in this situation, so AZS blocks containing 15% ZrO2 is used.
4)The crown of the melting zone
In the horseshoe flame kiln, silica brick is used in the crown since it is cheap and has good creep resistance. However it has bad resistance to alkali gas. Since the the gas contains a high content of boron and alkali in the glass wool furnace, silica brick is easy to be corroded and needs regular maintenance. To achieve longer service life, AZS block containing 30% ZrO2 and specially sintered mullite brick are used.
5)Throat
The throat is the most easily corroded part in the glass wool furnaces and cannot be hot repaired, so it directly determines the service life of the furnaces. Currently, fused cast AZS 41# WS is generally used in the throat. Since the main erosion in the throat is mechanical erosion, for large-tonnage glass wool furnaces, AZS block containing 50% ZrO2 is used.
6)Checker work
The alkali and boron in the glass wool has severe corrosion to the magnesia bricks. The alkali and boron steam is easy to crystallize at 810-940℃. The viscous crystals are adhered to the uneven checker work bricks and cause stoppage. The checker work usually adopts basic bricks, 97 or 98 magnesia brick in the upper part, 95 or 96 magnesia brick in the middle part and magnesia chorme brick and low porosity fireclay brick in the lower part. This is economic, but the service life is short. To expand the service life of checker work, the criss-cross fused cast AZS block is preferred.
The selection of refractory materials is the key to the benefits of glass wool furnaces. When selecting refractory materials, many factors should be taken into account, such as the service life, investment and production cycle.
Send an Inquiry
E-mail : sales@sunriserefr.com
Phone : +86-371-63838939 / Fax:+86-371-63835539
Company Address : No.36 Fengchan Road Of Zhengzhou, Henan, China (Mainland)
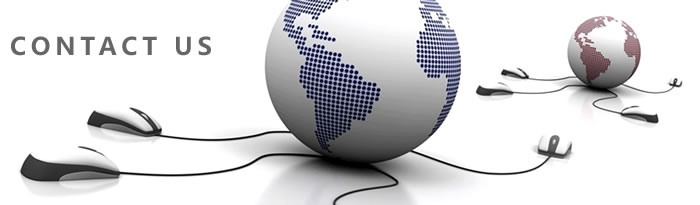
If you have any needs our help or are interested in our products, you can click online advisorychat with us online, or call our customer service telephone: 0086-0371-63838939. We will sincerely serve for you!
Product Category
- Fused Cast AZS
- Fused Cast AZS Block
- Fused Cast Skid Rail Block
- Fused Cast High Zirconia Block
- Fused Cast AZS Block
- Fiber Products
- Insulation Series Brick
- Fireclay Brick
- High Alumina Brick
- Corundum Brick
- Sillimanite Brick
- Mullite Brick
- Zircon Mullite Brick
- Zircon Brick
- Magnesia Brick
- Silica Brick
- Fused Cast Alumina Block
- Glass Mould Brick
Refractory Knowledge
moreCase
UAE to our factory inspection bri
...
Venezuela customer AZS fused bric
Venezuela customer AZS fused float glass furnace br...