Structure And Refractory Selection Of The Float Glass Furnace
Date:2016-05-17 18:02 From:Zhengzhou Sunrise Refractory Author:sunrise
The float glass furnace is used for the production of float glass which is a kind of glass made by floating molten glass on a bed of molten metal (typically molten tin often referred to as a tin bath).
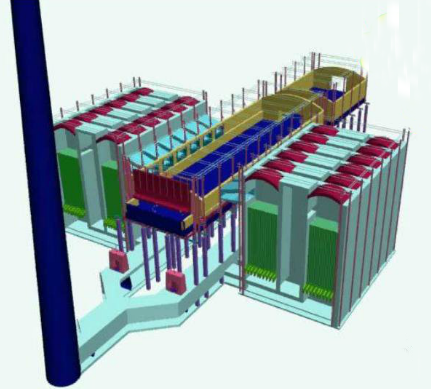
A float glass furnace includes a melting furnace which heats raw materials to form a molten glass batch, a working end where the molten glass batch is cooled, and regenerators which introduces heated combustion air into the melting furnace through a port neck.
The melting furnaces consists of the melting zone and refining zone or the upper space and the lower pool. The upper space is also known as the flame space, which consists of the front wall, the surface of the molten glass, the large crown and the breast wall. The lower pool is made up of the bottom and the sidewall.
The front wall spans across the feeding pool to block the hot gas and flame. Due to the corrosion of the flame and the batches, it is easily damaged and deformed. The front wall always adopts high quality silica brick, mullite brick and sintered AZS brick.
The breast wall should have enough strength. The hook brick is the key part to block the flame. In theory, as long as the corrosion resistance of the breast wall is good enough, it will not affect the service life of the glass furnace. The breast wall of the melting zone employs fused cast AZS 33#, while the breast wall of the refining zone can use high quality silica brick.
The crown determines the service life of the glass furnaces. The large crown composes the flame space with the breast wall and the front wall. The silica brick is generally used in the crown. In the oxygen-fuel furnaces, fused cast alumina block is used in the crown due to its good alkali vapor resistance.
The tank bottom is required to have good wear resistance and good integrity. The multi-layer bottom structure is always adopted. The first layer that is in direct contact with glass liquid is fused cast AZS block. Beneath the first layer lies the fireclay bricks. Between the two layers are AZS ramming mass.
The sidewall is built on the fireclay brick of the tank bottom. It suffers severe corrosion from the liquid glass. Currently, the float glass furnaces always adopt large AZS 33# block, which has no transverse joints and good corrosion resistance.
The throat is between the melting furnace and the working end for installing the cooling water and the stirrer and isolating the airflow of the melting furnaces. The structure of the throat always adopts low arch structure and hanging wall structure. AZS 41# is always used in the throat.
The structure of the working end is almost the same to that the melting furnace but simpler. The refractory materials used in this area varies depending on the glass produced. For high quality glass, the sidewall block and bottom paving block adopt alpha fused cast alumina block. Beneath the bottom paving block, alpha beta fused cast alumina ramming mass is used. Those refractory materials have low blistering potential and low pollution to the glass. The breast wall and the large crown always adopt high quality silica brick.
The regenerator is made up of top arch, the sidewall, the end wall, the partition wall and checker work. The top arch of the regenerator in the float glass furnace is always built with high quality silica brick. The sidewall, the end wall and the partition wall always adopt low porosity fireclay brick in the lower part, and basic refractory materials in the middle and upper parts. The checker work is the most important structure of the regenerator. It adopts low porosity fireclay brick in the lower parts, direct-bonded magnesia brick in the middle part, 95 magnesia brick in the upper part and 97 magnesia brick or sintered AZS brick in the top part.
Zhengzhou Sunrise is a refractory material supplier from China, offering high quality refractory materials for glass furnaces, including fused cast AZS block, fused cast alumina block, mullite brick, zircon brick, alumina bubble brick, magnesia brick, sillimanite brick, corundum brick, low porosity fireclay brick, high alumina brick, all kinds of glass furnace ramming masses, etc..
Send an Inquiry
E-mail : sales@sunriserefr.com
Phone : +86-371-63838939 / Fax:+86-371-63835539
Company Address : No.36 Fengchan Road Of Zhengzhou, Henan, China (Mainland)
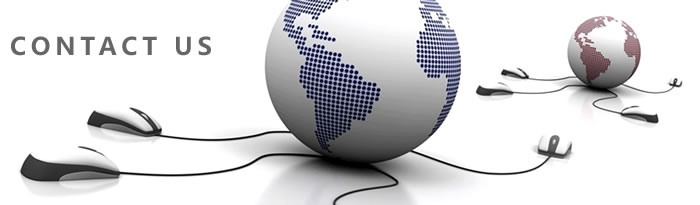
If you have any needs our help or are interested in our products, you can click online advisorychat with us online, or call our customer service telephone: 0086-0371-63838939. We will sincerely serve for you!
Product Category
- Fused Cast AZS
- Fused Cast AZS Block
- Fused Cast Skid Rail Block
- Fused Cast High Zirconia Block
- Fused Cast AZS Block
- Fiber Products
- Insulation Series Brick
- Fireclay Brick
- High Alumina Brick
- Corundum Brick
- Sillimanite Brick
- Mullite Brick
- Zircon Mullite Brick
- Zircon Brick
- Magnesia Brick
- Silica Brick
- Fused Cast Alumina Block
- Glass Mould Brick
Refractory Knowledge
moreCase
UAE to our factory inspection bri
...
Venezuela customer AZS fused bric
Venezuela customer AZS fused float glass furnace br...