Glass Defects And Fused Cast AZS Exudation And Corrosion
Date:2016-05-17 17:53 From:Zhengzhou Sunrise Refractory Author:sunrise
Glass defects are typically unavoidable. Common glass defects include bubbles, stones, knots, cords and cat scratches. Glass defects caused by fused cast AZS generally include two causes: exudation and corrosion.
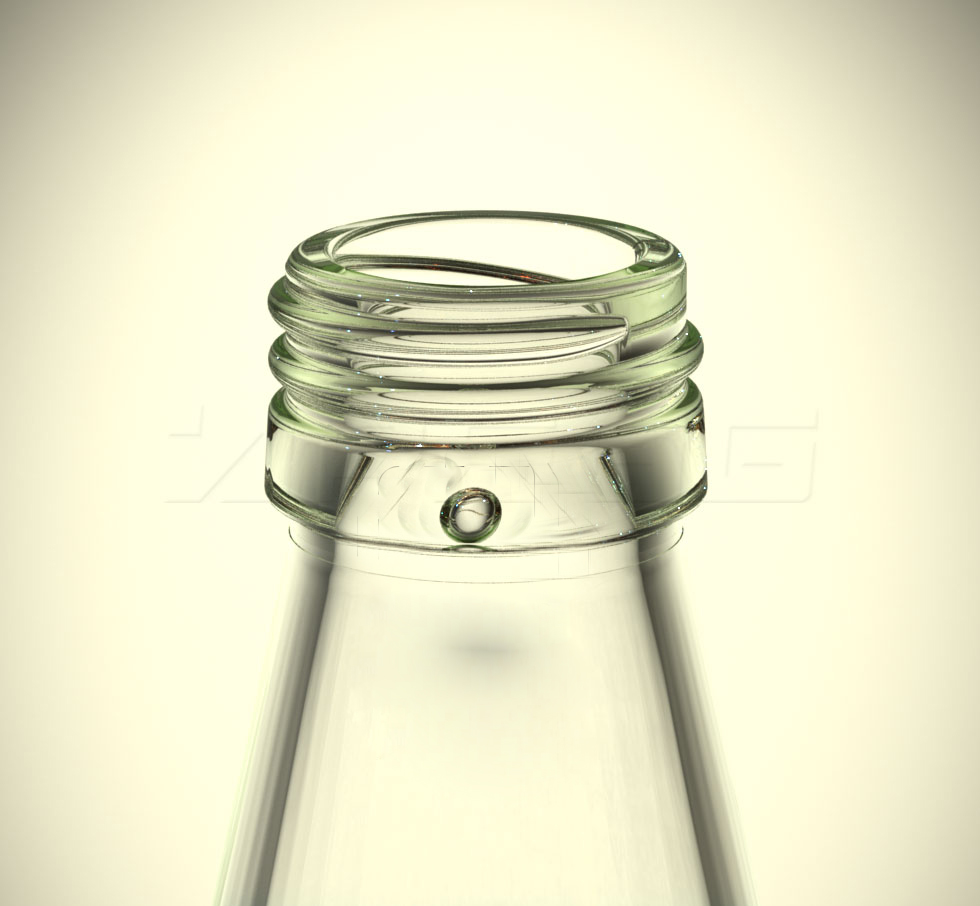
Corrosion of glass contact and superstructure refractories is the main reason for formation of undesirable glass defects. Fused cast AZS block is the most widely used refractory in glass contact areas and superstructure. Exudation is thought as the leading cause of knot and cord defects. It is only a short-term cause of glass defects. Corrosion is a more potent and long-term cause of defects.
Fused cast AZS consists of corundum, baddeleyite and a small amount of glass phase. The matrix glass phase surrounding the crystal phases of corundum, baddeleyite and their eutectic crystal, is likely to exude under a high temperature condition. Such exudation of matrix glass causes glass defects, such as glass knots or cords directly, and stones or blisters indirectly.
Both glass contact and superstructure corrosion of AZS block can lead to knot/cord defects. Glass corrosion can lessen with time due to boundary layer formation and the effect of external cooling at the metal line. Superstructure corrosion is a more potent and long-term source of defects and can continue through the entire campaign duration.
The superstructure corrosion is caused by several factors: flame, high temperature, batch carryover, evaporation of alkali, temperature variations and high stressed situation like oxy-fuel firing. Those factors result in the exudation of the glassy phase at beginning of campaign and corrosion of the refractories during the campaign which may cause glass defects.
All AZS block experiences an expansion of the glassy phase volume due to superstructure corrosion and can therefore serve as a source of liquid phase rundown, promoting glass defects. The glassy matrix phase in the block provides pathways for the corrosive alkaline and alkaline components to diffuse into the body of the block. This in-diffusion promotes the can result in an expansion of the glassy phase volume.
Therefore, the best solution is to avoid using AZS refractories in the superstructure lining of air fuel furnaces altogether. One alternative is a alpha-beta fused cast alumina block, which contains a very small amount of glassy phase (~2% by volume). Alpha-beta alumina block superstructure corrosion in air-fuel and oxy-fuel furnaces has significantly lower chemical alteration than that of AZS. Fused Cast AZS with modified chemistry and glassy phase can also be used as a alternative materials to lower defect potential.
Sunrise provides different grades of fused cast AZS blocks including AZS 33#, 36# and 41#. The products adopt superior materials, with process by special arc furnace forming it and cause low pollution to glass liquid.
Send an Inquiry
E-mail : sales@sunriserefr.com
Phone : +86-371-63838939 / Fax:+86-371-63835539
Company Address : No.36 Fengchan Road Of Zhengzhou, Henan, China (Mainland)
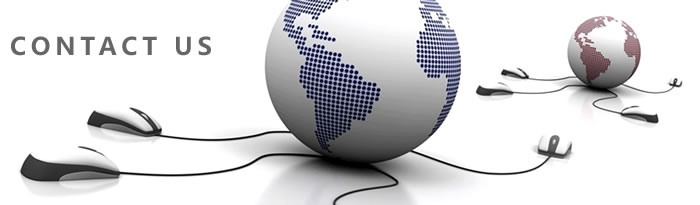
If you have any needs our help or are interested in our products, you can click online advisorychat with us online, or call our customer service telephone: 0086-0371-63838939. We will sincerely serve for you!
Product Category
- Fused Cast AZS
- Fused Cast AZS Block
- Fused Cast Skid Rail Block
- Fused Cast High Zirconia Block
- Fused Cast AZS Block
- Fiber Products
- Insulation Series Brick
- Fireclay Brick
- High Alumina Brick
- Corundum Brick
- Sillimanite Brick
- Mullite Brick
- Zircon Mullite Brick
- Zircon Brick
- Magnesia Brick
- Silica Brick
- Fused Cast Alumina Block
- Glass Mould Brick
Refractory Knowledge
moreCase
UAE to our factory inspection bri
...
Venezuela customer AZS fused bric
Venezuela customer AZS fused float glass furnace br...